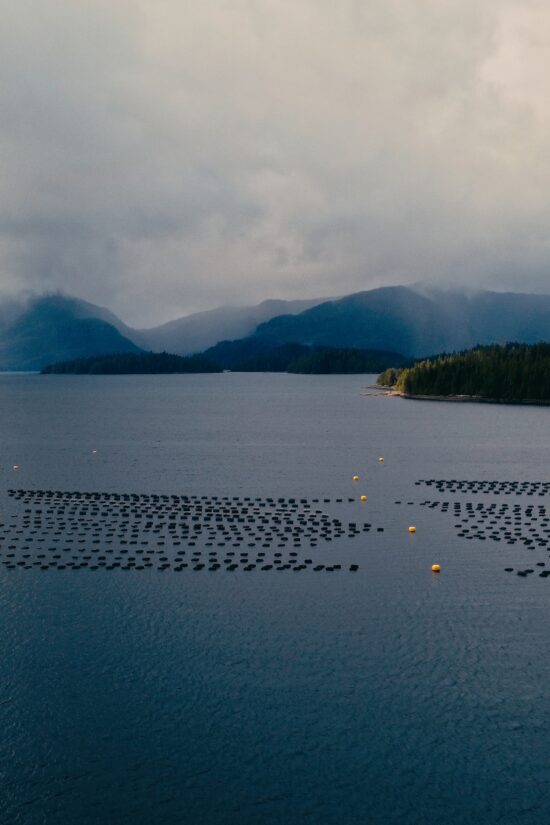
Alaskan farmers use various methods for the grow-out phase, depending on their site characteristics, natural resources, and permitted surface area. Various husbandry techniques are being developed and refined to maximize yields, minimize mortalities, and achieve optimal shell shapes and meat content.
Alaskan oyster farms range from small-scale family operations with custom-made equipment to larger-scale industrial sites implementing automated modern cultivation practices and state-of-the-art gear designed for scaled production.
Handling
Farm maintenance and routine handling protocols are essential for adequate oyster growth. Grading, sorting, and tumbling are done mechanically and manually to achieve labor efficiency and top-quality, well-shaped oysters, according to the farm's size and market needs. Tumbling helps oysters develop a harder shell and deeper cup by removing brittle edges. This also gives them an ideal uniform shape, which they would not be able to achieve on their own if grown in an overcrowded bag without regular movement.
Oyster meat content, shelf life, and shell attributes are interconnected and challenging to deal with separately. Final product quality will depend on the farming practices applied from the hatchery stage onward, with particular attention paid to densities and handling frequency.
Biofouling and predators
Biofouling is a major issue for any farmer, and if left untreated, it can significantly reduce oyster growth, quality, and survival. Each location presents a different composition of fouling organisms, and farmers constantly monitor these fouling events and decide on the appropriate ways and schedules to handle them.
Due to the abundance of nutrients in their flesh, oysters provide a wholesome and attractive meal for many natural predators. Depending on the type and density of the predators in the area, this could have a notable negative economic impact.
Four types of organism interactions and corresponding responses
Water flow blockers
- Organism example: Sponges, colonial tunicates, algae, and seaweed.
- Effect: Limit the flow of water through the cage, bag, or chamber.
- Prevention & control: Washing, manual removal, air drying
Predators
- Organism example: Sea stars, crabs, sea otters
- Effect: Eat the entire oysters or cause oysters to shut their shells and stop feeding.
- Prevention & control: Sufficient depth off the bottom, manual removal, enhanced cage close mechanisms
Competitors
- Organism example: Blue mussels, barnacles
- Effect: Compete with oysters for food and space
- Prevention & control: Timely washing, according to mussels' larvae life cycle, air drying, hot dipping, manual removal, and tumbling.
Beneficial
- Organism example: Sea urchins, sea cucumbers
- Effect: Provide biological control by eating algae, sponges, and other organisms.
- Prevention & control: Not necessary - keeping several sea urchins in each tray/bag can be used to clean the bags as well as the oysters.
We put these sea urchins in our trays, and they act as little Roomba vacuum cleaners, cleaning not only the trays and keeping them free of other undesired biomass but also cleaning the oysters themselves for inherently much better-looking oysters.
Cultivation systems
Farmers often blend several cultivation systems during the grow-out phase, depending on their farm location and surroundings. They utilize 2D systems like floating cages or beach culture and 3D systems suspended in the water column, leveraging each method's benefits and advantages to get the best possible results. Farmers report positive outcomes when starting in floating systems, followed by suspended culture, and with the option of finishing off in beach bags before harvest.
Vertically integrated business model from nursery to sales
Case study Alaska Shellfish Farms LLCSpecies: Pacific oyster
Capacity: Sales of ~1 million oysters per year
By having the farm site and FLUPSY close to shore, all automated grading, sorting, and processing gear on floating rafts that can be towed to the farm, Greg and Weatherly Bates operate a sturdy and efficient oyster supply chain.
Notable features
- Has a FLUPSY, suspended trays in a floating raft and long lines, and processing and handling platforms in the exact location for a streamlined supply chain.
- Located in Halibut Cove, the farm is nourished by glacier-fed waters, making the oysters more minerally and milky.
- Has been operational for 17 years, and won the 2020 Alaska Farm Family of the Year award.
- Offers fresh oysters for direct B2C sales off the dock in Homer and for returning customers in the lower 48.
The biggest floating flip cage farm in Alaska
Case study SeagroveSpecies: Pacific oyster
Capacity: 5 - 6 million oysters per year
Seagrove farms 27 acres in Doyle Bay, using the OysterGro flip cage system, which is durable and requires minimal labour.
Innovations & approach
Notable features
- A unitized system with standard cages enable the farm to produce six million oysters, with only four staff members and minimal contact with the oysters.
- Cages are either exposed to the air to clear biofouling or submerged in the feeding position at the top 1-2 feet of water, which is the warmest with good feed availability.
- Oysters are distributed evenly inside the cage bags (as opposed to suspended trays in rafts), allowing equal exposure to the feed through the currents. This results in consistent growth and much lower dead loss.
- Seagrove's ambition is well represented by its strategy of investing in high-efficiency, large-capacity gear and equipment to eliminate technical or technological bottlenecks once it decides to scale the operation. This strategy is reflected across all stages of its supply chain.
High quality oysters out from a small-scale family farm
Case study Tommaso Shellfish FarmsSpecies: Pacific oyster
Capacity: 80,000 - 100,000 oysters per year
Small-scale family farming is the backbone of the Alaskan oyster industry, demonstrating the mariculture lifestyle job with highly professional husbandry practices and premium oyster production.
Innovations & approach
Notable features
- One of four farms to form a cooperative in the Naukati area in Prince William Sound in order to improve near-farm processing capacity.
- Marketing various oyster sizes according to demand from May to October: 300-400 dozen a week for local buyers and restaurants in other regions, such as Anchorage, Juneau, and more.
- Efficient, low carbon footprint operation, with all required equipment on site for a highly effective growing and processing workflow operated with only 2 employees, handling all processes from spat to sale.
Joint Innovation Projects
Part of the AMC’s Research and Development Grant Component.
Optimizing the tumble culture method to improve Pacific oyster quality, and reduce labor
This project aims to optimize the tumble culture method for Pacific oyster farming in Southeast Alaska by reducing labor, improving oyster quality, and increasing yield. While tumble cages have proven successful in other regions for enhancing oyster growth and shape while minimizing labor, previous attempts in Alaska have been hindered by turbulent conditions.
This project aims to address these challenges, as well as uneven growth, and reduce sea star predation by designing Alaska-specific tumble culture gear that can withstand rough conditions, utilizing innovative mounting techniques to control cage motion. By collaborating with engineers, oyster farmers, and a biologist, the project seeks to test and refine the tumble culture method at three oyster farms in Southeast Alaska, potentially revolutionizing oyster farming practices in the region.